Sustainable solutions with Raspberry Pi
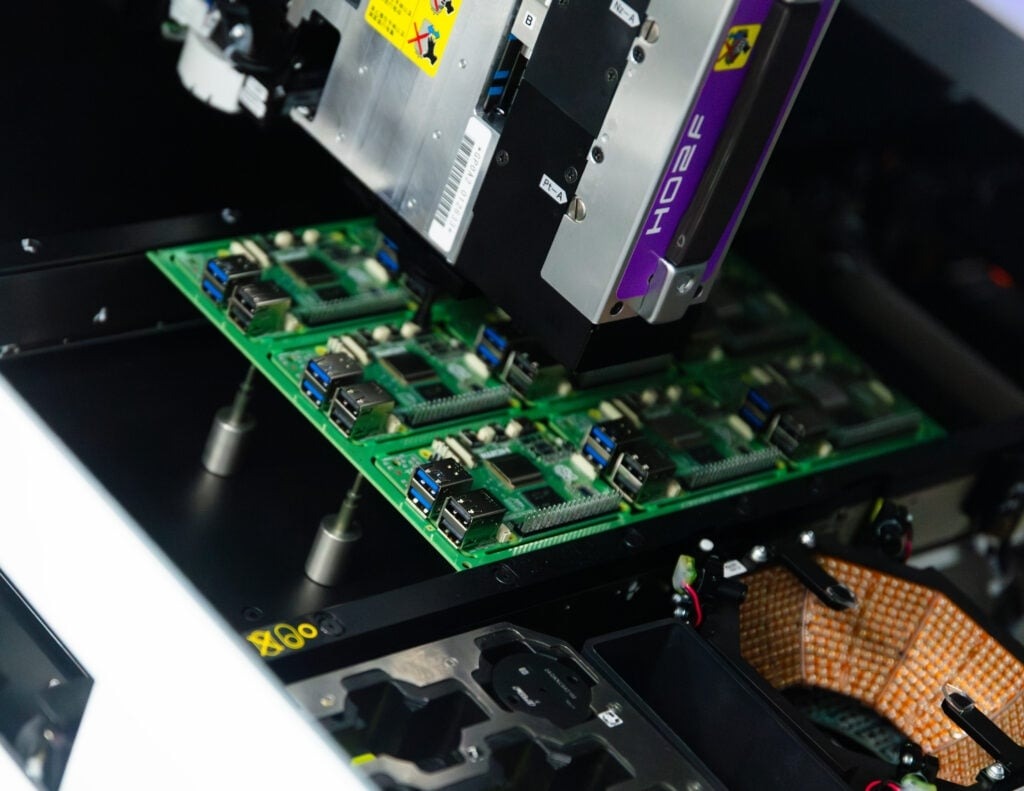
Written by Roger Thorton
We’ve reduced product returns by half, cut our manufacturing time by 15%, and eliminated 43 tonnes of CO₂ emissions per year by changing the way we solder connectors onto our computers.
In product design and manufacture, small changes often drive big differences in environmental impact, and at Raspberry Pi we’ve always made sure we have a thorough understanding of the processes used to manufacture our products so that we can spot ways to improve them. In the run-up to Raspberry Pi 5, we worked with our manufacturing partner Sony to implement a technique called intrusive reflow soldering, an adjustment that has improved product quality, reduced waste, and lowered our environmental impact.
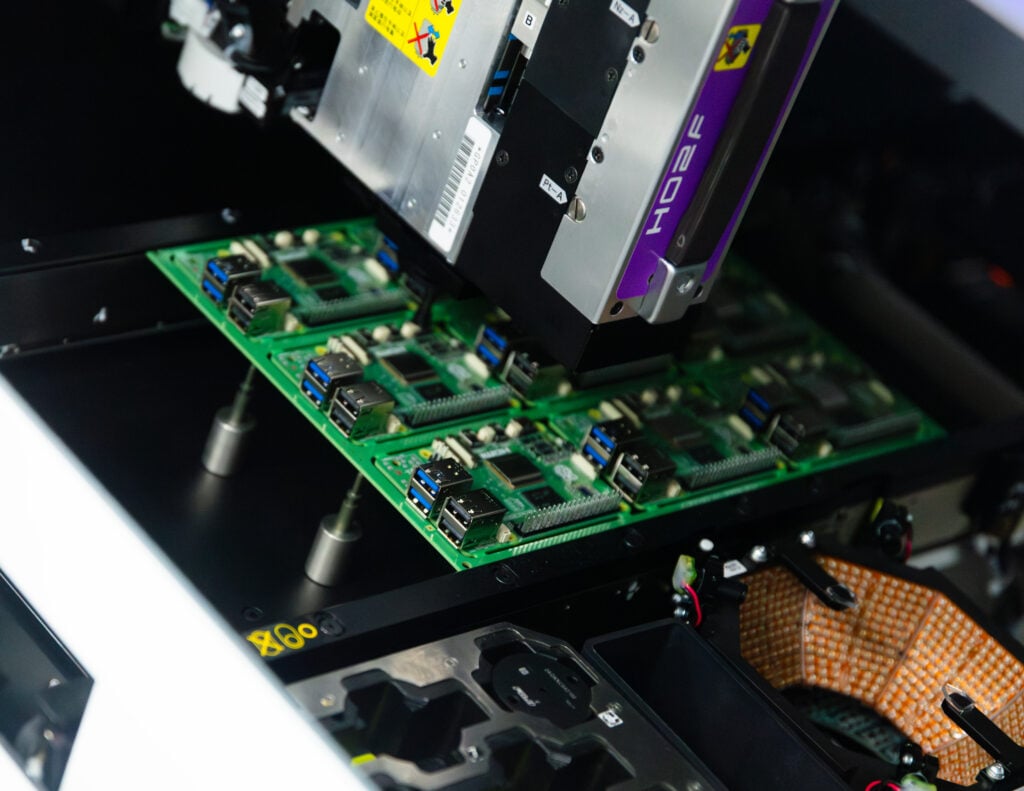
Solving the through-hole bottleneck
Through-hole connectors have long been a sticking point in efficient production. They require robust solder joints made through the printed circuit board itself, meaning they can’t simply be handled by the standard processes used with SMT (Surface Mount Technology, aka pick-and-place) machines. Because of this, we have always endeavoured to minimise the number of through-hole parts, and this type of mounting is typically reserved for connectors. In the early days of Raspberry Pi, these parts were inserted by hand, and later by robotic placement. There then followed a wave soldering step — an additional process involving a molten solder bath which the boards pass through. This added time, cost, and complexity to our production line.
Thanks to our work with Sony, we have eliminated all of the through-hole–specific actions from our manufacturing processes. With intrusive reflow, we can now place through-hole connectors using the same pick-and-place machines we already use for surface-mount parts; this means there is no longer any need for bespoke robotics, or for an additional soldering stage. Over a series of trials, we perfected component placement, tweaked the solder paste stencil, refined the PCB layout, adapted the connector design, and adjusted the inspection process. We validated the results against our stringent quality control, successfully achieving all the standards that we set ourselves.
July 22-23, 2025
Hyatt Regency, Minneapolis, MN
A new manufacturing standard for Raspberry Pi 5 and beyond
This became the production process that we have used on all Raspberry Pi 5 computers, and we’re working to roll it out to the manufacture of our earlier models too.
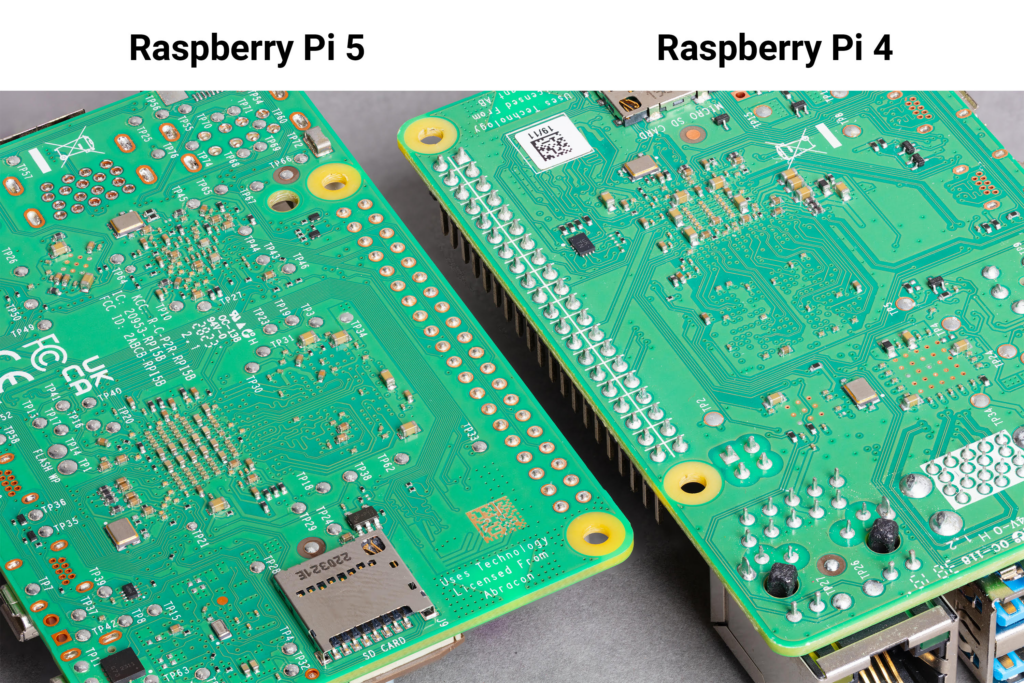
The change delivered a marked increase in product quality, with a massive 50% reduction in product returns. It also increased the speed at which products are manufactured by 15%. Work In Process (WIP) inventory was eliminated entirely, as there is no longer any break in the production line, all the way from bare boards coming into the factory to finished Raspberry Pi computers being packaged into boxes. And removing a set of machinery — the selective solder bath — from the production line reduced the CO₂ output of our production by 43 tonnes per year.
Smarter manufacturing, smaller footprint
Raspberry Pi’s move to intrusive reflow soldering shows how targeted changes in manufacturing can lead to significant improvements in sustainability. By cutting energy use, eliminating wasteful intermediate steps, and improving product quality, we’re reducing our environmental impact while making our production more efficient. It’s one of many ongoing efforts to manufacture more responsibly and more sustainably.
Leave a Reply