Revolution on the Factory Floor: How Automation is Redefining the Future of Manufacturing
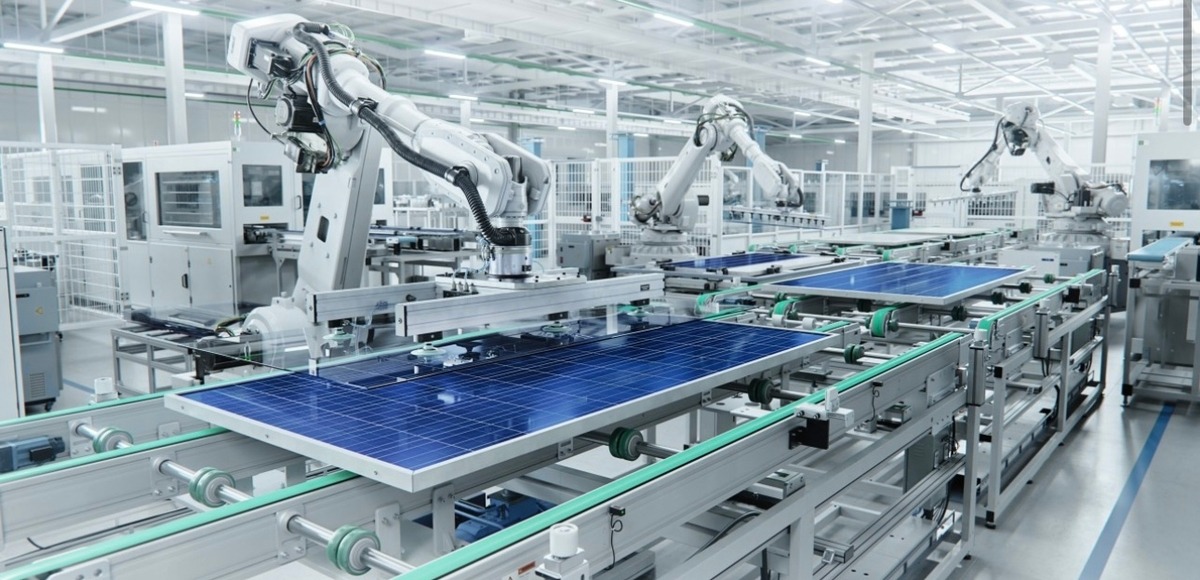
Revolution on the Factory Floor: How Automation is Redefining the Future of Manufacturing
Automation has been a cornerstone of manufacturing since the advent of the Industrial Revolution, as a foundation for manufacturing improvements in productivity, quality and efficiency. The modern smart manufacturing age began through technological enhancements which include artificial intelligence (AI) and robotics together with the Internet of Things (IoT). The transformative changes affect both production operations and the worldwide industrial sector.
The Evolution of Manufacturing Automation
Manufacturing automation developed through different periods that brought successive transformations to industrial productivity and operational efficiency. The path of automation demonstrates that perpetual innovation and technological advancement because of accumulated development from simple mechanization all the way to smart manufacturing.
1. Mechanization (First Industrial Revolution)
During the late 18th century, the first industrial revolution started as humans transitioned theircwork to machine-based production from manual labor. The implementation of water-powered machines together with steam engines transformed the textile industry alongside agriculture. The production transition enabled factories to operate at greater speeds and cut their dependence on both human workers and animals. Modern manufacturing developed through mechanization because machines demonstrated their capacity to boost production efficiency.
2. Mass Production (Second Industrial Revolution)
Mass production entered the world through the second industrial revolution during the late 19th century and early 20th century to substantially enhance production systems. Henry Ford established assembly lines in the automobile sector which enabled rapid and consistent mass production of products. The adoption of electric power displaced steam engines enabling production to become more reliable at the same time it became easier to scale operations. Standardizing both parts production together with operational processes emerged as an essential element which lowered expenses while boosting product volume.
3. Digital Automation (Third Industrial Revolution)
Computer and electronics technologies gave birth to the third phase of manufacturing automation during the mid-20th century. Programmable logic controllers (PLCs) helped manufacturers implement automated machinery control which minimized the need for human involvement in repeated work procedures. Robotics introduced itself as a crucial element within production lines which increased accuracy while decreasing faults. Digital automation came to replace mechanical automation thus permitting manufacturing operations to become more flexible while attaining greater efficiency.
4. Smart Manufacturing (Industry 4.0)
The current manufacturing era we now inhabit under the name of Industry 4.0 leads businesses towards self-directing and completely networked production systems. Through IoT technology and artificial intelligence and cyber-physical systems machines achieve data analysis as well as self-operating capacities and electronic communication capabilities. Smart factories enhance production performance in real-time through optimized systems which bring increased effectiveness alongside lower product waste and improved customized output. Industry 4.0 supports predictive maintenance because this feature allows equipment to operate more efficiently while requiring less maintenance downtime. Manufacturing advancement will probably center on two elements along with automation development and AI-driven decisions making combined with sustainable production practices. This industrial revolution evidence shows that businesses must adopt technological changes to succeed against market competitors working in evolving manufacturing industries.
Key Technologies Driving Automation in Manufacturing
The industry transformation in manufacturing depends on various state-of-the-art technologies including:
Artificial Intelligence and Machine Learning: The applications of Artificial Intelligence and Machine Learning utilize extensive dataset analysis to generate process optimization and maintenance prediction as well as decision intelligence. Manufacturers benefit from AI automation through operational enhancement while also attaining decreased human mistakes and enhanced decision quality. Between 2020 and 2030 AI will add between $3.7 trillion as direct revenue to global manufacturing and supply chain operations annually.
Advanced Robotics: Modern robots combine sensors and artificial intelligence technologies which allow them to execute detailed complex operations with great precision while achieving adaptable results. The integration of collaborative robots known as cobots enables human workers to work safely alongside each other thus boosting productivity at the workplace.
Internet of Things (IoT): Manufacturers benefit from Internet of Things (IoT), because its connected devices monitor and share manufacturing floor information to display real-time data about equipment functioning alongside product availability and processing activities. This connectivity facilitates proactive maintenance and efficient resource management.
3D Printing (Additive Manufacturing): Through 3D Printing technology, businesses can generate fast prototypes and produce hard-to-make shapes which traditional manufacturing procedures cannot produce. The technology speeds up the product creation period to support customized solutions.
Impact on Manufacturing Processes
Modern manufacturing processes experience a complete revolution through the implementation of these modern technologies.
1. Predictive Maintenance: AI analyzes real-time operational data which leads to equipment failure predictions so manufacturers minimize their downtime by 30% and transition to proactivity rather than reactivity for their maintenance operations.
2. Quality Control: The combination of machine learning and AI-powered cameras performs quality control by detecting defects with high accuracy to minimize waste and boost product quality.
3. Supply Chain Optimization: Supply Chain Optimization occurs through automation because it helps enhance both demand forecasting methods and inventory control systems alongside logistics operations to create faster and more effective supply chains.
4.Customization and Flexibility: The advanced nature of automation systems helps manufacturers rapidly change production lines between runs, which makes possible both market-driven personalized production and fast response capabilities.
Case Studies of Automation in Action
Xiaomi's "Dark Factory": Xiaomi established its "Dark Factory" at Changping China where automated robots utilize AI to build smartphones, which means one phone manufactured every single second without human assistance. The dark factory proves that automation systems operate at levels of efficiency and precision previously unattainable.
BMW's Collaboration with Figure Robotics: BMW established a strategic alliance with Figure Robotics to launch humanoid robots across their production areas, thus improving operational efficiency. Improved robotic systems increase their operational speed by 400% while being able to place automatic auto parts with excellent precision at 1,000 daily operations.
Cellares' Cell Shuttle: The Cell Shuttle from Cellares represents a biotech start-up invention which develops robotic systems to produce automated cell therapies. Cellares' Cell Shuttle represents an innovative technology that seeks to improve both affordability and accessibility in cell therapy manufacturing.
Challenges and Considerations
The substantial benefits of automation require various challenges to be overcome. The growing adoption of automated processes leads to job loss situations mainly affecting tasks that perform repetitively. The Tasmanian Cadbury factory announced plans to eliminate 20 positions because it will implement automated systems which will make operations more efficient and update its production methods. The workforce must develop programming expertise and data analytical capability and equipment maintenance competence, because these abilities have become essential for the job market. Fundamental investment in relevant educational and training courses needs to address the present skill deficiency. Because manufacturing now depends on higher amounts of connectivity, there are additional risks appearing across cyber security fronts. The defense of intellectual property together with operational integrity demands businesses to deploy solid cybersecurity protocols. The high price of advanced automation technology systems creates an obstacle for small and medium-sized enterprises (SMEs) to implement these solutions. Manufacturing costs initially rise with new infrastructure yet the future performance maximization usually provides satisfactory return on investment.
The Future of Manufacturing Automation
The path of manufacturing automation leads to escalating smart and self-operating production systems. Humanoid robots are currently being developed to perform the same tasks which humans traditionally handle. At Flowery Branch Georgia's warehouse, Digit robots from Agility Robotics execute duties that involve obtaining and moving bins through conveyor belts. AI algorithms will perform advanced real-time decisions for optimized production operations including resource planning without requiring human personnel. Production sustainability improves through automation which decreases resources waste while maximizing energy effectiveness while creating environmentally friendly products efficiently. Automation enables supply chains to respond rapidly to disruptions which strengthens their overall resilience during outbreaks and natural disasters occurring across the globe.
Conclusion
The manufacturing industry experiences a fundamental change due to automation which generates enhanced operational efficiency and precise production practices and industrial progress. Manufacturers need continuous adaptation to advanced technologies including AI robotics and IoT because they drive future business success in this progressively automated sector. Complete achievement of automation requires companies to maintain equilibrium between developing their workforce with technological innovations and protecting against cybersecurity threats while handling ethical concerns. Public institutions and business sectors need to work together to establish policies which provide unemployed workers opportunities for introductory programs and protect their rights during professional realignment. Sustainable industrial growth depends on intelligent automation, because it enhances human productivity through expertise collaboration resulting in improved manufacturing operations. Successful business advancement during the Fourth Industrial Revolution depends on strategic acceptance of upcoming technological changes
Leave a Reply