The Hidden Risk: How Cybersecurity Impacts Operational Continuity in Automation
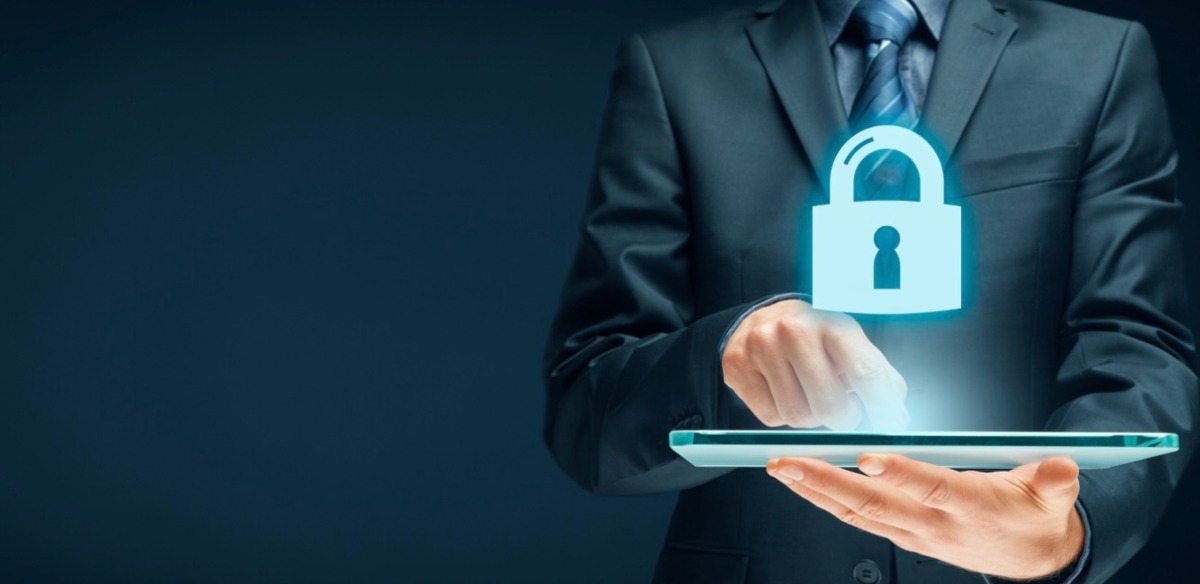
The Hidden Risk: How Cybersecurity Impacts Operational Continuity in Automation
Introduction
The industrial revolution called Industry 4.0 has revolutionized manufacturing operations and transportation systems and energy production methods through automation, which improves efficiency along with productivity. Industrial systems which now depend heavily on linked networks face new cybersecurity problems. Protecting all elements of Industrial Control Systems presents the essential requirement to sustain critical infrastructure safety and operational stability.
Understanding Industrial Control Systems (ICS)
The supervision and control of ICS rely on three distinct mechanisms: Supervisory Control and Data Acquisition (SCADA) systems, Distributed Control Systems, (DCS) and Programmable Logic Controllers (PLC). The systems operate in multiple sectors of industry to monitor and manage operations across power generation, as well as manufacturing facilities. IT integration with OT boosts operational efficiency but creates larger danger areas against cyber-attacks. Operational Control Systems face cyber threats, which result in process interruptions and financial damage and endanger human safety alongside these operations. Industry automation requires protective cybersecurity frameworks composed of network divisions, alongside recurring system update practices and employee education to protect
against state-of-the-art threats.
The Growing Threat Landscape
The combination of information technology with operational technology enables Industrial Control Systems to come under increased cyber threat attacks. These systems operated in isolation before modern times so they had minimal risk exposure to cyberattacks. Because ICS networks interface with digital technologies they are now at risk of experiencing the same threats, as typical IT networks such as malware attacks and ransomware intrusions and advanced persistent threats (APTs).These cyber events show that these threats represent serious problems because:
1. Stuxnet (2010): This sophisticated worm dubbed Stuxnet (2010) attacked Iran’s nuclear facilities by manipulating PLCs which led to significant physical destruction.
2. Industroyer/CrashOverride (2016): A power grid failure in Kyiv Ukraine occurred when Industroyer/CrashOverride (2016) malware executed its attack. This incident established that electricity supply can be affected by cyberattacks.
3. Triton/Trisis (2017) displayed the risk of safety instrumented systems being targeted when it attacked Saudi petrochemical facilities and threatened lives. The series of attacks demonstrates that modern industrial automation systems deal with enduring advanced cyber risks which show no signs of ending.
Recent Cybersecurity Incidents
The number and complexity of attacks targeted at industrial automation systems have increased rapidly during recent times. Cybercriminals have started to take advantage of security weaknesses in old systems and poor authentication practices and complex digital network connections. Industrial cyber incidents have become more common and sophisticated during recent times as exemplified by multiple new occurrences.
1. The number of cyberattacks against U.S. utility providers experienced a 70% escalation above 2023 rates (The Guardian 2024). The fast digitalization of power grids alongside using outdated software has exposed systems to increased vulnerability against cyberattacks thus
driving up breach incidents.
2. Ransomware Attack on KNP (2025): The 158-year-old logistics company KNP was shut down by Russian hackers who gained access through its vulnerable password (2025). Merely one week after the server takeover the attackers demanded millions but their actions resulted in substantial financial plus operational setbacks.
3. In 2024 TSA introduced cybersecurity regulations that apply to pipelines along with railroads which specified quick cyberattack notifications, along with yearly cybersecurity assessments for critical infrastructure management. Industrial automation requires immediate improvement of cybersecurity systems to prevent destructive disruptions of operations.
Key Vulnerabilities in Industrial Automation
Multiple security issues affect industrial automation systems because of increasing digital complexity in their operations. The key vulnerabilities include:
1. Stand-alone systems make up many Industrial Control Systems (ICS) which depend on outdated technologies without security features from newer technology generations. These systems underwent no initial development for connectivity purposes which makes them susceptible to cyber-attacks.
2. The separation between control system networks and IT systems remains insufficient, allowing cyber attackers to exploit weak points in order to breach critical operational infrastructure. Attacker success in infiltrating an IT system enables them to move into important OT environments that results in disruption of industrial operations in these areas.
3. Industrial automation bases its functions on external suppliers, since it requires their equipment and software support alongside maintenance services. System vulnerabilities result from weak cybersecurity measures among external entities that work with critical infrastructure thus making these facilities more exposed to attacks.
4. People who work for the organization are essential for cybersecurity defense, but their poor attention to security creates significant threats for the system. Through password weaknesses and social engineering methods along with phishing attacks cybercriminals can successfully enter ICS network systems. Inadequate regular cybersecurity education programs lead to higher chances of system breaches.
Certified Motion Control Professional Program
Strengthen Your Skills and Enhance Your Career
Motion control is ubiquitous to automation. A3 offers the fundamental knowledge that benefits everyone working with motion control, motors and automation technologies. The program is designed to ensure professionals have the knowledge they need to advance their careers and benefit their businesses.
Become a Certified Motion Control Professional (CMCP) and join the elite group of system integrators, machine builders, manufacturers, end-users and others recognized in the industry for their professional knowledge and expertise.
5. Industrial automation systems commonly operate without modern cyber monitoring solutions which creates problems in detecting and responding to present threats. Unmonitored cyberattacks persist unnoticed over extended periods because of which severe harm results. These security gaps need a comprehensive cybersecurity plan which features recent system updates alongside network partitioning, as well as robust access rules and supplier security checks alongside constant employee training to defend systems against threats.
Best Practices for Securing Industrial Automation Systems
Organizations need to create purpose-fit cybersecurity plans for industrial environments to reduce cyber risks.
1. Complete risk assessments must be executed regularly to detect threats facing ICS operations and direct prevention solutions according to threat seriousness.
2. IT networks need to be separated from OT networks through implementation of Network Segmentation to prevent breaches from spreading across the infrastructure.
3. User and system accessibility should be limited to essential operational rights through the Principle of Least Privilege for reducing attacks on compromised accounts.
4. IT personnel should keep their systems updated with the latest software versions and firmware to handle security issues, but need to maintain control of critical operations throughout the update process.
5. The organization must provide consistent training to employees, which includes instruction about both cybersecurity best methods and phishing detection along with proper password policy maintenance.
6. The organization must create and conduct tests of their cyber incident response plans, which must establish detailed steps along with communication strategies and step-by-step recovery instructions.
7. Implement an audit system through intrusion detection technology, which must continuously check for anomalous activities to generate swift and appropriate responses. The implementation of these procedures leads to substantial improvements in industrial automation system cybersecurity defenses.
The Role of International Standards
Industrial automation system protection depends heavily on following international cybersecurity standards. The IEC 62443 series functions as an internationally accepted set of standards which delivers extensive direction about securing Industrial Automation and Control Systems (IACS). This standard includes essential sections about risk assessment and component requirements, along with system design to facilitate organizations using a structured cybersecurity method. The implementation of technical standards permits various industries to execute established security methodologies, which globally improves their defensive ability against cyber threats. Two security frameworks namely NIST’s Cybersecurity Framework (CSF) and ISO/IEC 27001 function as essential tools to develop secure industrial systems.
Future Challenges and Considerations
Industrial automation development causes new cybersecurity challenges to emerge which require immediate attention.
1. Integration of Emerging Technologies: New vulnerabilities emerge from the increasing adoption of Internet of Things (IoT) devices and the implementation of cloud computing, as well as the utilization of AI-driven automation. Modern technologies enhance exposure points in industrial networks making security protection stronger, through encryption methods and access control protocols and segmented network architecture.
2. Sophistication of Cyber Threats: Industrial networks experience sophisticated cyberattacks because cybercriminals perform attacks using AI-powered malware, together with ransomware-as-a-service and deep fake social engineering tactics. Businesses need to improve their cybersecurity protection by using real-time surveillance along with sharing threat data and preparing active incident reaction strategies.
3. Regulatory Compliance: The worldwide cybersecurity regulations face permanent changes in their rules and requirements. Laboratories must remain knowledgeable about current industry regulations which includes NIS2 Directive for EU members and U.S. critical infrastructure cybersecurity rules to meet compliance standards and prevent compliance violations. Prior preventive measures will fundamentally protect the security and operational efficiency of industrial automation systems during future emerging cyber threats.
Conclusion
The protection of critical infrastructure demands cybersecurity measures in industrial automation, because it guarantees both operational safety and system reliability and continuous operations. The rise in complex cyber attacks demands industrial organizations to develop better cybersecurity systems while adding sophisticated threat detectors with security awareness programs across the workforce. An organization constructs robust cyber protection against threats by maintaining secure operations standards in combination with worldwide security protocols and routine protocol updates. A protected industrial automation future will develop through the strategic partnerships of governmental bodies and security professionals alongside leadership within industrial sectors. The advancing nature of industrial automation requires cybersecurity systems to develop in parallel to ensure safety of physical objects supported by digital assets
Leave a Reply