Fueling the Future: Real-World Case Studies of Smart Control Solutions Transforming the Oil & Gas Industry
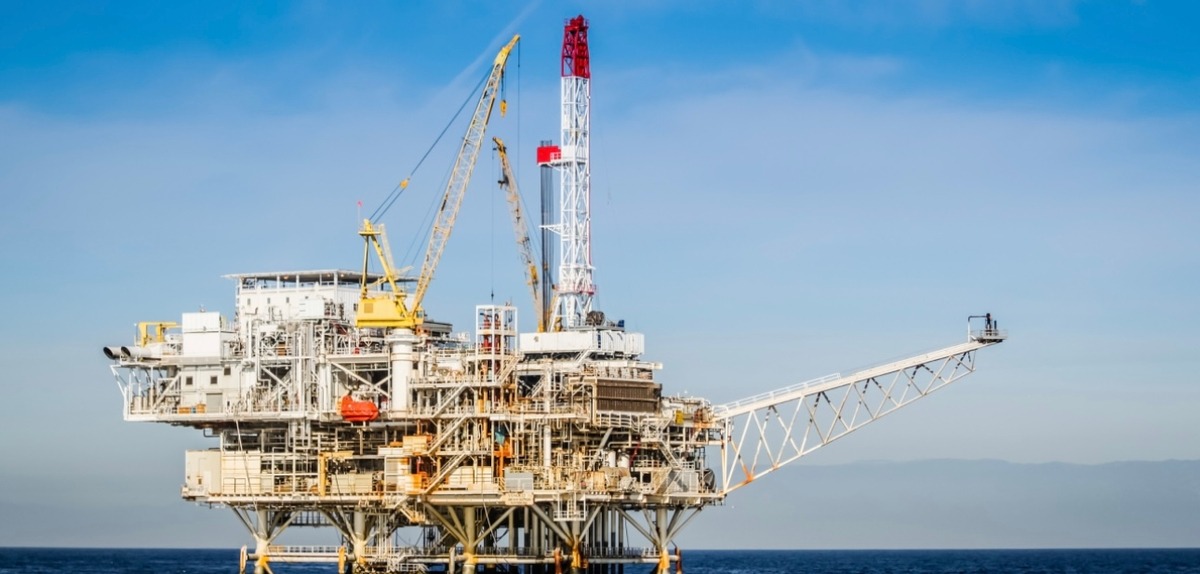
Fueling the Future: Real-World Case Studies of Smart Control Solutions Transforming the Oil & Gas Industry
Introduction
Digital technologies now lead a major change within the operationally complex industry that involves high-risk investments because of oil and gas exploration. Multiple advanced control systems bringing digital twins, artificial intelligence, and remote monitoring capabilities allow organizations to change their operational procedures.
The innovations deliver benefits that extend beyond convenience by achieving maximum production optimization, while reducing downtime incidents, lowering operational expenditures, and boosting security levels This article examines practical examples, showing leading industry companies utilize these technologies to reach efficiency goals and maintain competition in the evolving energy marketplace.
1. BP’s Digital Twin and AI Integration
The APEX system developed by BP allows operational simulation of real-time production
systems across all its international facilities through digital twin technology. Engineers utilize these platforms to evaluate proposed modifications of systems and anticipate operational outcomes and discover problems, which otherwise could become major issues. When exclusively analyzing performance in 2017, the APEX platform resulted in an additional daily production output of 30,000 barrels per day.
Operations-based choice-making at BP received additional strength through their venture with Palantir Technologies. The artificial intelligence tools together with large language models (LLMs) evaluate substantial historical data collections, to present field engineers with intelligent suggestions and predictive data points that help execute real-time operational decisions.
2. Equinor’s Echo Platform
Equinor as the Norwegian energy giant created the digital twin platform "Echo" to assist project development stages starting from the initial design phase up to daily operational functions. The Johan Sverdrup oil field received Echo as one of Norway’s biggest oil facilities where the platform saw implementation. The platform provides one common digital space where engineering staff along with operating teams and logistics members collaborate jointly. Echo provides its users the ability to visualize facilities virtually through augmented reality (AR) features. The early detection of safety threats enables proper training methods that ultimately generates safer operations in the field.
3. The Shell company uses digital twins alongside predictive maintenance
Shell uses digital twin technology throughout numerous offshore assets to boost their
maintenance capabilities. Virtual models from the company show real-time equipment visibility, which enables the organization to recognize forthcoming failures beforehand.
By using predictions for maintenance, the organization reaches better asset durability while also extending operational safety time and reducing downtime incidents.
The partnership between Shell and Akselos resulted in an extension of life for their Southern North Sea 50-year-old platform. The digital replication of the platform enabled Shell to pinpoint required upgrades which extended operational duration by 20 more years. Using this method the platform became more reliable and prevented future costs which would have been needed to develop a brand new platform. Shell implements predictive maintenance practices which establishes new criteria for operational efficiency, risk reduction, and enhanced production management.
4. Eni’s VR-Powered Rig Simulation
Digital twin technology at Eni enables VR integration for better operational planning and worker training across their facilities. Eni's staff adopts complex drilling operation experiences through virtual reality simulations of the Scarabeo 8 ultra-deepwater rig before executing them in real environments. Through its approach, the organization enhances strategy development by pinpointing potential difficulties and ensuring staff readiness to handle challenges without endangering personnel. Through VR-based digital twins Eni boosts both staff training and operational effectiveness thus creating safer operations in risky environments.
5. Devon Energy’s AI-Driven Drilling Optimization
The drilling operations at Devon Energy benefit from artificial intelligence technology to increase horizontal drilling precision. The company deploys AI algorithms to examine subsurface information while these algorithms guide drilling tools accurately across challenging geological structures. The technology allows Devon Energy to perform more efficient drilling so they reach 25% higher well productivity. The enhanced drilling precision at Devon Energy creates better drilling quality and lowers operational expenses. AI technologies enable efficient decision processes which lead to prompt
problem-solving thus keeping operations timeframes normal and optimizing total efficiency for well construction. This technological advancement produces more than productive operations because it simultaneously creates safer drilling situations. Better path precision control during drilling operations lowers the risk of severe and dangerous mistakes that would lead to high costs. Through its artificial intelligence-based drilling approach Devon has become an industry leader for operational accomplishment.
6. Chevron’s AI-Powered Drones for Remote Monitoring
The deployment of artificially smart drones by Chevron serves remote pipeline and offshore platform monitoring functions as well as protects critical infrastructure facilities. The drones use computer vision technologies that automatically identify gas leaks and equipment malfunctions and structural problems as they occur in real-time operations.
The drones represent an automated monitoring solution for Chevron which substitutes
dangerous inspections performed by humans. By using unmanned aircraft systems Chevron reduces both hazardous exposure risks to employees and accelerates maintenance responses which lowers operational interruptions and keeps vital infrastructure active.
7. Tyrion Integration’s SCADA Platform
Tyrion Integration released the smart SCADA platform “Nucleus” which enables cost-efficient automation for the oilfield industry. Nucleus operates in the Permian Basin to provide cloud-based communication abilities and integrate systems efficiently while reducing costly hardware requirements. The system helps small operators alongside startups keep track of their fields using a flexible affordable tool for efficient monitoring and control.
8. The digital twin concept helps ExxonMobil optimize its liquefied natural gas
(LNG) facilities. Through the adoption of digital twin technology ExxonMobil enhances the performance of its liquefied natural gas (LNG) production operations. The virtual models duplicate every stage of the LNG product chain including natural gas flows, cooling mechanisms, and storage management and shipping operations.
Continuous data monitoring in combination with predictive analytics enables ExxonMobil to project market demands and identify logistical bottlenecks along with simulating operational stresses before actual events occur. Such forward-planning techniques enable LNG processing facilities to minimize operational
stoppages, while delivering safe and consistent operational results. Such digital twins gain improved operational decisions and maintenance schedules through the implementation of machine learning algorithms which capture information from previous system performance.
9. LLOG Exploration’s Subsea Monitoring
LLOG Exploration utilizes digital twin technology to monitor its complex subsea infrastructure and infrastructure components throughout operations in the Gulf of Mexico as an independent offshore oil and gas company. These digital twins keep an ongoing watch on underwater pipelines and valves along with deepwater components by delivering environmental data in real time as well as predictive analytics.
The system detects pressure anomalies and leaks together with structural weaknesses at an early stage which helps avoid significant incidents that occur in dangerous environments. Digital transformation of subsea operations at LLOG enables the company to prevent disasters and minimize unexpected interruptions of operations, thus improving maintenance scheduling capabilities. Small operators now gain access to advanced safety protocols usually maintained by larger companies because of this technological advancement. Future Trends and Industry Implications New control system innovations drive transformative changes in oil and gas operations while several upcoming breakthroughs await in the next few years.
These upcoming five years will establish:
✓ Autonomous drilling rigs utilizing AI decision systems will enhance drilling precision together with reduced human manual interaction.
✓ The integration of essential blockchain systems ensures safe asset tracking along with
equipment systems and logistics because they stop fraudulent behavior while improving operational performance.
✓ Digital twins enable carbon capture excellence through their ability to monitor and optimize storage systems, because they support time-based analytics for sustainability achievements. The implementation of real-time environmental sensors enables companies to track environmental factors and emissions both reactively and proactively, in order to guarantee compliance while lowering environmental effects. Cutting-edge cybersecurity measures exist to defend centralized control systems that link
various components together by protecting operational data from cyber threats.
The new technologies enable independent operations based on data which unite operational efficiency with safety measures and environmental sustainability. Oil and gas companies will reach precise sustainable operations through their use of AI alongside blockchain technologies combined with real-time data analysis.
The energy sector will benefit from advanced intelligent sustainable solutions which will become standard practice during the future period.
Conclusion Digital control systems have become imperative for the oil and gas industry. Oil and gas organizations need to adopt digital control systems as a necessity.
These case studies show how early adopters including ExxonMobil and LLOG together with BP and Devon Energy obtain quantitative improvements in operational efficiency, as well as enhanced safety standards and increased profitability.
These technological advancements represent more than mere instruments since they act as catalysts for changing the entire oil and gas industry. The ongoing adoption and development of these technologies by companies will result in an intelligent and better protected and environment-friendly energy sector.
Leave a Reply