AUTOMATION TECHNOLOGY OBSOLESCENCE AND ITS IMPACT ON ORIGINAL EQUIPMENT MANUFACTURERS
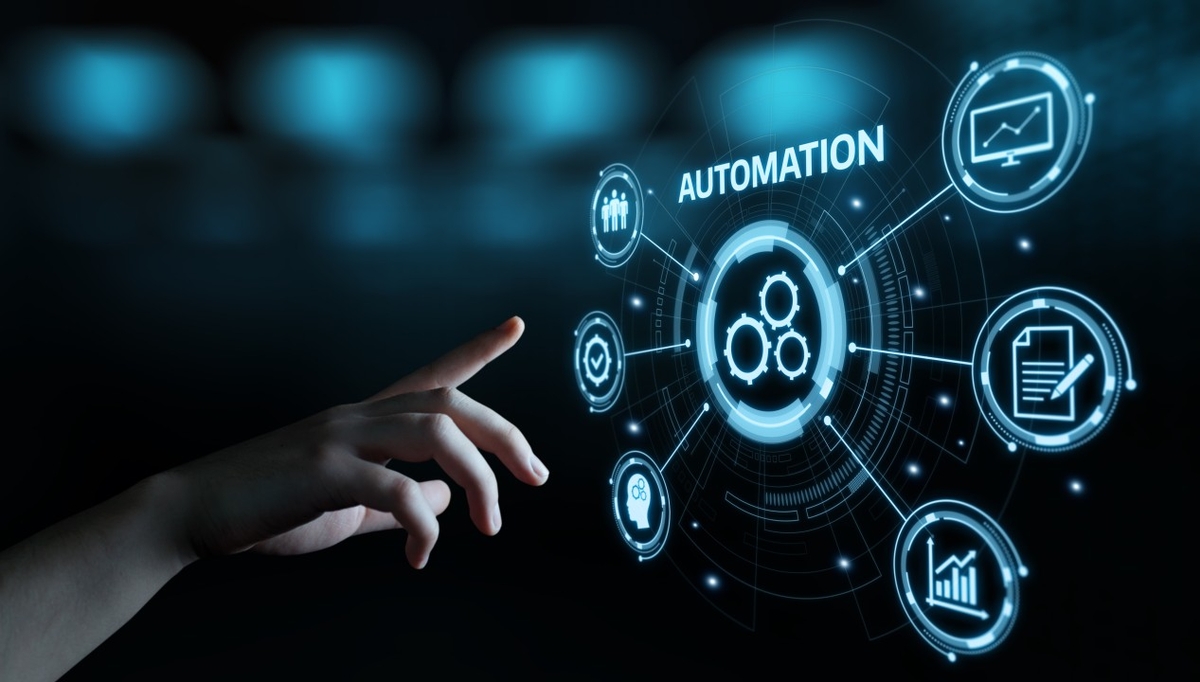
Automation technology obsolescence refers to the fast pace by which automation technology, equipment and software become outdated, demanding constant upgrades and replacements.
Automation technology obsolescence is becoming a reality faced by many manufacturers who have adapted to the possibilities of automation technology.
This has posed significant challenges for original equipment manufacturers (OEMs), who must conform and innovate to remain competitive.
In this article, we will be exploring the effect of automation technology obsolescence on OEMs and discuss strategies for addressing this problem.
But before we go into that, let us take some time to understand the concepts of OEMs.
ORIGINAL EQUIPMENT MANUFACTURER (OEM)
An Original equipment manufacturer (OEM) is a company whose goods are used as components in the products of another company, known as a value added reseller (VAR). The VAR works closely with the OEM, which often customized designs based on the VAR’s needs and specifications. (Source: Investopedia.com)
For example, an OEM computer manufacturer might make computers for a brand like Dell or Lenovo, who then sells the products under their own brand names (Source:toolsense.ip)
OEMs manufacture parts to sell to VARs. Although some OEMs make complete items for a VAR to market, they usually don't determine the finished product.
An OEM may create electronic compartments for a huge company like Samsung, then Samsung as the VAR, makes a high definition TV.
OEMs focus on business to business sales, while VARs target the general public or end consumers.
Different parts of cars such as exhaust systems or brake cylinders are also manufactured and constructed by OEMs.
UNDERSTANDING AUTOMATION TECHNOLOGY OBSOLESCENCE
The breakthrough pace of technological advancements and development is breathtaking.
Unique technological innovations emerge every few years, thereby rendering existing equipment and software obsolete.
This quick obsolescence cycle affects all aspects of automation, from programmable logic controllers (PLCs) to robotics and machine learning(ML) algorithms .
With the emergence of industry 4.0 and the rapid growth of modern technology, obsolescence is a definite roadblock for many manufacturers.
Issues can range from an outdated control platform, availability of critical spares, or lack of support from an existing supplier.
The changing demands for a machine may also render it obsolete, for instance if the previous machine seems to have a higher output rate.
IMPACT ON OEMs
Automation technology obsolescence has consequences for OEMs.
Obsolete technological equipment and software can give rise to decreased productivity, increased maintenance costs, and decreased product efficiency and quality.
Therefore, OEMs that fail to adapt to new technologies risk losing market share and damaging their reputation.
The inability of OEMs to address obsolescence is severe. OEMs that fail to upgrade or develop their equipment's and software may experience
- Reduced productivity
- Increased maintenance costs
- Decreased product quality
- Loss of market share
SOLUTIONS FOR OEMS TO CONTROL AUTOMATION TECHNOLOGY OBSOLESCENCE
Here are some strategies for Original Equipment Manufacturers (OEMs) to reduce automation technology obsolescence:
1. Modular Design: Design equipment with modular components that can be easily upgraded or replaced as technology advances.
2. Technology Road mapping: Plan and forecast technology advancements to ensure equipment is designed with future compatibility in mind.
3. Regular Upgrades: Regularly update and modernize equipment to prevent obsolescence and maintain compatibility with newer technologies.
4. Open Architecture: Use open architecture designs that allow for easy integration with newer systems and technologies.
5. Standardization: Standardize equipment and components to simplify upgrades and reduce customization costs.
6. Collaboration: Collaborate with technology partners to stay up-to-date with the latest advancements and ensure equipment compatibility.
7. Life Cycle Management: Implement life cycle management strategies to manage equipment throughout its entire life cycle, from design to decommissioning.
8. Training and Support: Provide ongoing training and support to ensure customers can effectively use and maintain equipment.
9. Upgrade Paths: Offer upgrade paths for existing equipment to extend its life and reduce electronic waste.
10. Refurbishment: Offer refurbishment services to breathe new life into older equipment, reducing waste and minimizing the need for new purchases.
11. Technology Insertion: Insert new technologies into existing equipment to enhance performance and extend its life.
CONCLUSION
In conclusion, the challenges of automation technology obsolescence looms large over OEMs, threatening to render their products and services obsolete.
However, encouraging a culture of continuous innovation, fostering collaborative relationships, and prioritizing regular upgrades and modernization, OEMs can not only mitigate this risk but also leverage it as a catalyst for growth and transformation.
As the industry continues to hurtle forward at high speed, the importance for OEMs to conform, to be innovative, and customer-centric has never been more pressing.
Will they rise to the challenge and redefine the future of automation, or will they succumb to the pitfalls of obsolescence?
Leave a Reply