Five Ways Automation Helps Manufacturers Hit Their Energy Efficiency and Sustainability Goals
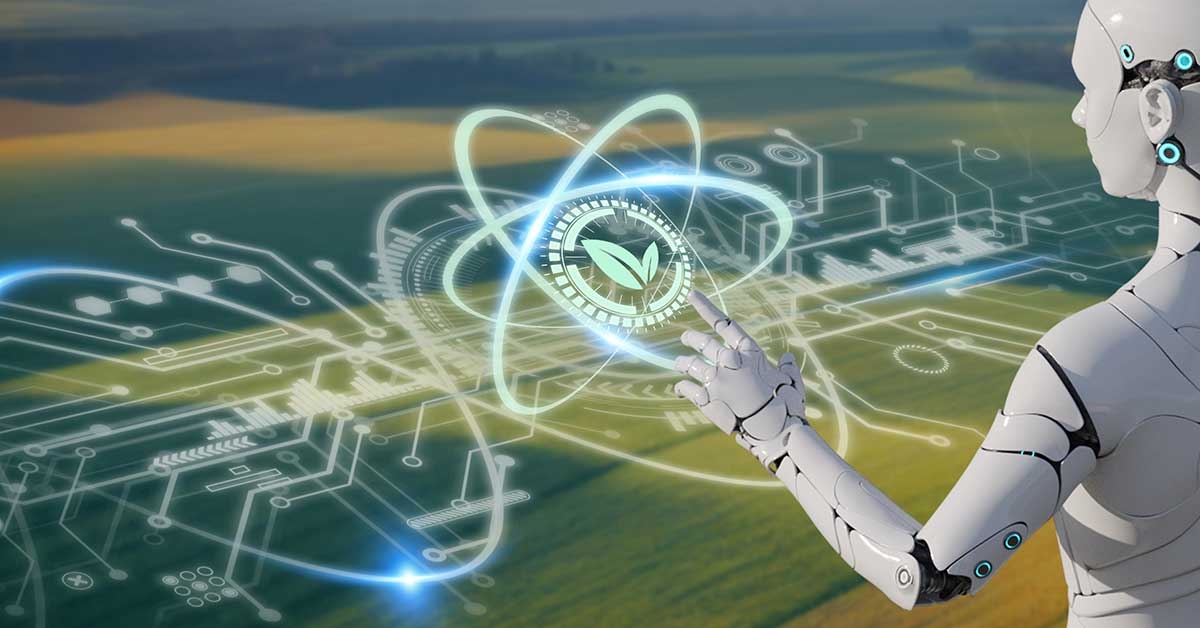
Industry generates nearly one-third of global CO2 emissions, primarily from energy use, Economist Impact recently reported. Despite past energy efficiency efforts, there’s a renewed push among industry leaders to address the current energy crisis and climate emergency by developing energy efficiency programs, including for use in manufacturing.
According to the International Energy Agency, the intergovernmental organization that provides policy recommendations, analysis, and data on the entire global energy sector, ongoing energy efficiency programs could potentially eliminate 70% of carbon emissions from the industrial sector.
For manufacturers, sustainable practices that minimize environmental impact and resource use are essential to address the energy and climate crises. Original equipment manufacturers (OEMs), for example, can differentiate themselves by offering “greener” machines that conserve energy while delivering much-needed flexibility and throughput. Automation technologies — including robotics, machine vision, and artificial intelligence — play a pivotal role in that effort.
Automation in Action
Automated manufacturing is inherently sustainable. It lets companies create processes that reduce negative impacts on the environment, which helps them to become more energy efficient and practice sustainability across various sectors. Let’s look at five ways automation technologies help increase overall equipment effectiveness and move energy efficiency and sustainability forward in manufacturing.
1. Optimizing production processes
Industrial robots can perform tasks fast, efficiently, and accurately across a wide range of industries. This reduces cycle time and minimizes energy consumption within manufacturing processes. Machine vision systems ensure accurate quality control, which helps prevent defects that could lead to energy-intensive rework or waste.
For example, devices — such as cameras, sensors, and software — can inspect products during production and identify defects or deviations from specifications. If a flaw is detected, the system can trigger automated adjustments, ensuring that only high-quality products proceed. This real-time quality control not only improves overall product quality but also reduces waste and the need for rework.
Take Elliptical Design, for example. The British design and manufacturing company partnered with TM Robotics to leverage industrial automation technology to improve traditional cheese cutting methods, which were proving to be inexact. To address this, Elliptical Design created an ultrasonic cutting system that harnesses microscopic blade vibrations to make precise cuts without damaging the product.
Along with the innovative ultrasonic cutting system, the integrated robotic system includes pick-and-place applications with vision and conveyor tracking. The robots handle the cheese block, moving it seamlessly through weighing and cutting stations. This automation replaces a previously manual process, reducing production time from four to five days to two days and achieving 83% waste reduction. This success underscores how strategic implementation of automation in manufacturing can significantly enhance efficiency, reduce waste, and streamline production processes.
2. Implementing energy-efficient equipment
With features such as regenerative braking and low-power modes, modern robotics systems — particularly battery-powered robots such as autonomous mobile robots (AMRs) — are designed to be energy efficient Today’s machine vision cameras and technologies do not require vast amounts of power, and at the same time, provide accurate and detailed information about the production process — reducing overall energy usage and improving quality.
3. Leveraging predictive maintenance capabilities
Many automation systems can be equipped with predictive maintenance technology, which identify potential issues before they become problematic or cause a breakdown — ultimately minimizing unplanned downtime. In addition, predictive maintenance helps optimize energy usage, since a well-maintained machine operates at maximum efficiency. Predictive maintenance ensures that processes, equipment, and inspection systems are operating at peak efficiency, which reduces the risk of energy-intensive failures.
4. Integrating energy monitoring systems
Advanced robotics can be integrated with energy monitoring systems, such as smart sensors and devices, to track and analyze energy consumption. When coupled with data analytics, monitoring energy usage over time provides manufacturers with insights into their consumption patterns that help them zero in on areas for improvement and identify energy-saving opportunities. Then, they can implement strategies to optimize operations for energy efficiency.
5. Reducing waste through precision
Precise movements by robots reduce waste, use energy-efficient components, adapt to changing demands, and enable predictive maintenance. In the case of collaborative robots, robot precision also fosters a more energy-efficient and collaborative work environment. These factors collectively minimize material waste and energy consumption associated with rework.
Implementing some or all of these energy-efficient and sustainability technologies and practices is proving beneficial for many companies. Schneider Electric is just one example. After deploying a full digital transformation of its factories in 2017 — which included integrating automation and industrial software — the company improved operational efficiency by 12% in the first year.
Manufacturing a Better Future
Manufacturing automation isn’t just a strategic tool for businesses to achieve key performance indicators (KPIs) in corporate sustainability and environmental compliance. It’s also an effective and socially responsible way to move the needle on reducing the industry’s carbon footprint overall.
It can also have a positive impact on a company’s bottom line. Adopting energy-efficient practices has the potential to yield significant cost savings for manufacturers. The U.S. Department of Energy says that industrial energy consumes upward of 10% of a manufacturing company's operating expenses. By reducing their energy consumption, manufacturers can lower their utility bills and boost profitability.
With a blend of regulatory adherence and internal guidelines, manufacturers that leverage automation for energy efficiency and sustainability are seeing substantial cost savings and heightened operational efficiency, while mitigating the impact they have on the environment.
Leave a Reply